Cars and other forms of transportation are major contributors to the production of greenhouse gasses. Moreover, most automobiles have already released a lifetime’s worth of emissions before they even leave the factory parking lot. This has led to companies discovering new ways to actively reduce the amount of plastic waste they produce. In this article, discover how Faurecia researched to find alternative materials for plastic and the consequences it entailed.
Faurecia, one of the largest automotive part manufacturers in the world, had a unique outlook on the issue surrounding plastic and car pollution. Although Faurecia manufactures interiors, seating, and emission-reduction technologies for many car companies including Tesla and Mercedes-Benz, the company does not always have a say on how a car is produced and its usage. Because of this, Faurecia decided to aid in the reduction of emissions through the innovative techniques in the manufacturing of materials for automobiles. It was this perspective that resulted in Faurecia’s partnership with Schoolab’s “Deplastify the Planet” program.
Deplastify the Planet, a pioneering training program offered jointly by UC Berkeley (SCET) and Schoolab, is a global innovation studio where students work with real-world companies with one goal in mind: “deplastify” the planet.
Using the Design Thinking methodology, students are assigned to work in small teams on semester long projects. Each team is paired with a company for an entire semester whilst thinking, building, testing, and solving problems on a common issue which in this case: how to curb the excessive use of plastic. Design Thinking focuses on User & Market Research and Prototype development where the participants are constantly researching how to find a solution to the problem.
Faurecia’s new mission aimed to “depollute” its supply chain and its materials through localization. While alternatives to plastic exist, they involve significant cost tradeoffs and dramatic shifts in suppliers, complicating the supply chain and further exacerbating the emissions produced.
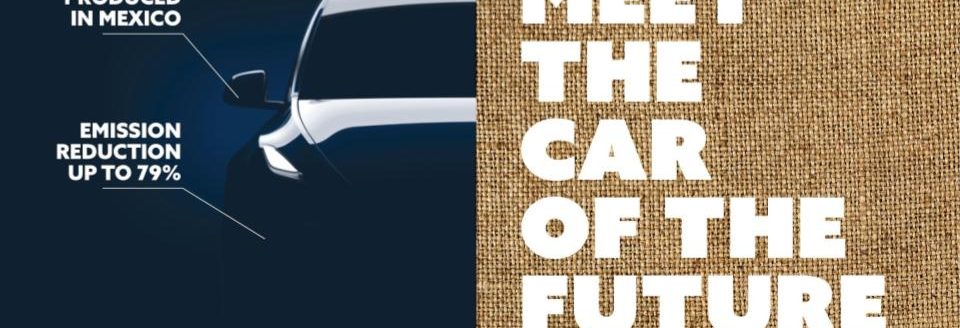
1st semester: Replacing plastic with a locally-sourced natural fiber
Starting as a team of six, the Berkeley students worked to find the best alternative to plastic that could be made and sourced locally using a natural fiber native to Faurecia’s manufacturing region in Mexico.
The solution resulted in a 50% plastic reduction, increasing overall recyclability of excess materials, drastically reducing supply chain emissions, and it even supported a local farming community that has been struggling for decades. As the first team of students worked to plan and develop this idea, they found nothing but support from the program’s partners and from Faurecia who invited 2 students to Mexico to be on site and become more involved in the process.
By the end of the semester, the students had identified a new fiber that met all the requirements, discussed the idea with potential suppliers and manufacturers, and talked to locals in Mexico about ways to support, innovate, and fund the local industry. Fully committed to facing environmental challenges, the company signed for another semester.
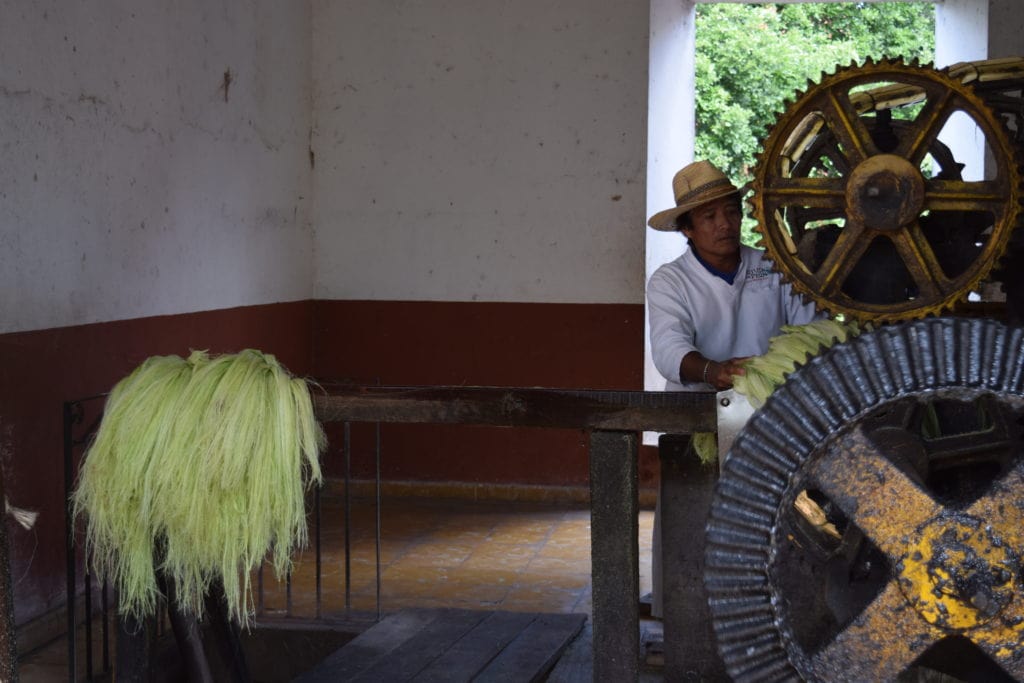
2nd semester: Prototyping a global supply chain
The main challenge that the students had to face was taking the plan they had developed and transforming it into a reality. In the first half of the process, the team brought together their supply and manufacturing partners in Mexico. The second half of the project revolved around creating an official prototype, testing the mechanics of the fiber, and determining the brand.
Unfortunately, as the month of March arrived, as did the commencement of a global pandemic, imposing formidable challenges on the horizon. Despite the obstacles the students and the program itself faced, the team was able to end the semester with a thorough plan on how to proceed with the project and how to bring about effective change, technological advances, and funding for the struggling local Mexican agriculture. They even created an international guide to replicate the process so that Faurecia’s clients would be able to work towards the localization of their own supply chains.
After two semesters of fresh perspectives and a committed team of UC Berkeley students, mentors, and professionals, Faurecia is now moving on to manufacturing a better and more plastic-free future, helping their clients learn, and committing to learning more themselves.
Thanks to this two-semester collaboration with Schoolab and SCET, the company broadened its perspective and diversity through the involvement of more technical engineers and native Spanish speakers. After 9 months of intense work, the project was ready to be introduced internally and implemented in their global locations beginning with South Africa.
The desire to collaborate with students created a more valuable and interesting experience for the corporation allowing them to demonstrate the steps that can be taken to deplastify the planet.